OVERVIEW In dry pet food manufacturing, the standard palatant application sequence typically follows three steps: (i) fat spraying, (ii) liquid palatant spraying, (iii) dry palatant application. Most fats must be heated (30-40 °C) to remain liquid. Once the fat is applied, palatants are usually layered on top, as depicted in...
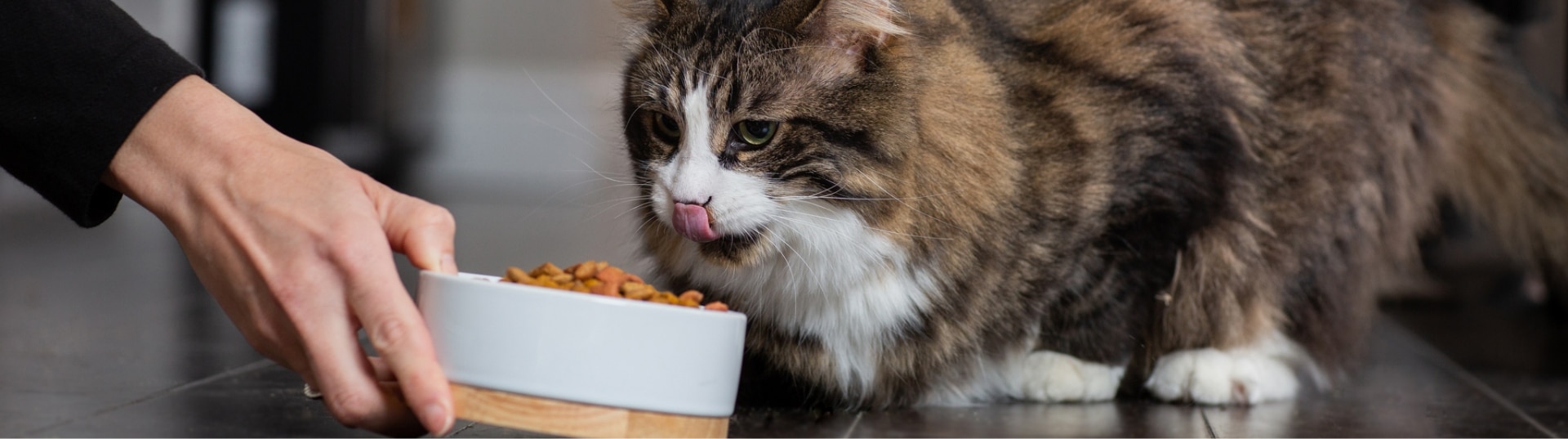
Palatants: Storage and Stability
DRY PALATANTS
Dry palatants are flowable powders that are that are used inside or applied topically to enhance the flavor profile of pet foods, treats and supplements. These low-moisture powders range in color from light tan to dark brown, have an attractive food safety profile, and can be shipped economically in standard or bulk bags.
BULK BAG STORAGE
The largest dry palatant package size is a woven polypropylene bulk bag or a big bag, sometimes called a Super Sac®. The weight of a bulk bag will vary depending on the bulk density of its contents. Generally, a bulk bag is around 2,000 pounds or 900 kilograms. In Europe, the maximum weight of a bulk bag is 1,000 kilograms. Dry palatant bulk bags have a bottom spout with a tie closure to allow the discharge of contents. In general, it is best to place these unloading systems away from the application point to both control dust and limit exposure to warm, humid conditions.
Bulk bags require that the pet food manufacturer have bulk material handling capabilities and equipment. This includes hoists, trolleys, hangars, and dischargers which come in many different designs and configurations. Bulk bags generally require less handling and are sometimes less expensive compared to the same product in a smaller package size.
STANDARD BAG STORAGE
Dry palatants are also available in smaller bag sizes. In Europe, multi-layered paper bags, also called valve bags, commonly contain 25 kilograms of dry palatant. The maximum size of a valve bag is 610 x 560 x 200 millimeters. In the US, multi-wall, poly lined, pinch bottom open mouth bags, also called kraft bags, contain 50 pounds of dry palatant. Kraft bags measure 16 x 4 x 36 inches. When full, the bags will vary in height depending on the bulk density of the specific dry palatant. Standard bags generally require more handling, but they don’t require specialized hoist and trolley equipment. These bags are simply dumped into the coating system hopper at the time of use.
Because dry palatants readily take up moisture, they should be stored in cool, dry areas.
STABILITY
The low water activity (Aw) of dry palatants offers an effective means to control microbial growth. Because dry palatants contain fats, they are also stabilized using antioxidants like tocopherols. Antioxidants are introduced as early as possible in the manufacturing process to ensure fat oxidation is controlled throughout the process.
If it becomes necessary to dispose of expired product, suggestions for disposal can be found in the Safety Data Sheet or by contacting the AFB Customer
Service team.
LIQUID PALATANTS
Liquid palatants are moderately viscous, low pH materials requiring specific storage and handling considerations. All product-contact surfaces should be constructed of 316 or 304 stainless steel, fiberglass or plastic. Carbon, steel and brass should be avoided. Liquid palatants should be well mixed prior to use to ensure optimal performance.
BULK STORAGE
Bulk shipments are typically 5,500 gallons or 20,000 liters and will arrive at 85-105°F/25-30°C. These shipments may be offloaded with an onboard pump or dedicated unloading pump. Bulk storage tanks should have a capacity of 8,000-10,000 gallons in North America and about 30,000 liters in Europe. They should be equipped with a high efficiency agitation system that minimizes air incorporation to prevent foaming and oxidation. Storage tanks should include provision to maintain temperatures 85-120°F/25-35°C to control viscosity.
To ensure optimal product performance, it is recommended that these products be used within 45 days of receipt.
Periodically (at least annually), bulk tanks should be completely voided, cleaned, and sanitized. A common cleaning procedure is a hot water rinse, followed by foaming with an alkaline-based solution, and rinsed with a no-rinse food grade sanitizer.
INTERMEDIATE BULK CONTAINER (IBC) STORAGE
An intermediate bulk container, or IBC, is a square corrugated shell surrounding a polypropylene bag covered with a corrugated top that holds approximately 2,500 pounds or 1,200 kilograms of liquid product. This container is also sometimes called a tote. The bag is treated with an antimicrobial agent to prevent mold growth at the product-bag interface. Containers may be stacked two high and should be stored in an area above 70°F/20-25°C. Prior to use, the IBC should be well mixed to ensure optimal performance. The most common mixing method is recirculation.
DRUM STORAGE
A 55 gallon or 200 liter drum is a standard drum with a polypropylene liner and cover. The liner is tied closed at the top to prevent air from entering the liner. The gathered liner is treated with an antimicrobial agent to prevent mold growth at the product-liner interface. If a partially used drum needs to be stored, be sure that the liner is drawn down, re-sprayed, and then re-tied to reduce air exposure.
Prior to use, liquid products stored in drums should be mixed well to ensure homogeneity. In cases where a drum product is moved to an intermediate tank prior to use, adequate mixing may be achieved at this point.
STABILITY
Liquid palatants are stabilized using different methods to ensure optimal performance during product shelf life. Proper product handling is an important part of ensuring this performance.
MICROBIOLOGICAL STABILITY
AFB liquid palatants are microbiologically preserved using potassium sorbate as the primary anti- mycotic, in combination with an AAFCO approved acidulant. As another option, AFB offers a natural preservative system that may be advantageous for a pet food manufacturer. These products will not support the growth of common food spoilage organisms like yeast and mold. The integrity of the preservation system must not be compromised or microbiological growth is possible.
Liquid products in IBCs and drums are best stored by minimizing air contact, thereby discouraging growth of aerobic organisms like molds. Drum liners should be collapsed and re-tied after use.
CHEMICAL STABILITY
Fat present in liquid products is chemically stabilized using antioxidants such as mixed tocopherols. Antioxidants are introduced as early as possible in the manufacturing process to ensure that fat oxidation is controlled throughout the process.
Excessive agitation and air incorporation into liquid products may compromise the integrity of the antioxidant system. Dilution or adulteration of liquid palatant products may destabilize the preservation systems being employed. These practices should be avoided. Contact the AFB Customer Service team for assistance should this occur.
If it becomes necessary to dispose of expired product, suggestions for disposal can be found on the product MSDS Sheet or by contacting the AFB Customer Service team.